This guide will help you understand the dynamics behind brushless drone motor used on quadcopters and how they influence flight characteristics. We’ll dive into types of motors, design variations, weight, total power and other factors affecting a quad motor performance. So let’s get started.
For beginners there are 2 types of motors used in drones: brushed and brushless motors. They vary in the way they work. The brushless is way more powerful for their weight than brushed motors, and they last way longer. For bigger quads: no question, brushless is king.
But for the micro and nano drones, it’s fantastic to have these cheap motors to crash with confidence.
The internal workings of a brushed and a brushless motor is the same; both are based on electromagnetism.
When the motor windings become energized (both the motors have coils), a temporary magnetic field is created that repels (and/or attracts) against the permanent magnets present inside the motor.
This magnetic force is creating the repulsive force in the coil that is used to spin/rotate the shaft.
DIFFERENCE BETWEEN BRUSHED AND BRUSHLESS MOTORS
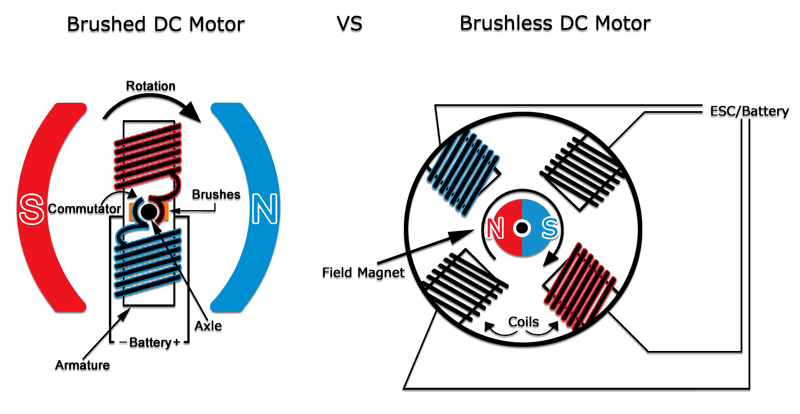
Efficiency wise, brushless motors are typically 85-90% efficient whereas a brushed DC motor is 75-80%. Windings are present on the rotor for a brushed motor as compared to in a stator for a brushless motor
This difference in efficiency means that more of the total power used by the motor is being turned into rotational force and less power is being lost as heat.
Brushless motor lasts longer because there are no brushes to wear out, while the brushed motor wears out quickly. That’s one of the reasons brushed motors came out cheaper then brushless motors.
This guide is mostly oriented on brushless motors used in racing/freestyle fpv drone configurations.
Name | Motor Size | kV | Cells (LiPo) | Config | Rate |
---|---|---|---|---|---|
Lumenier JB2407-7 2407 | 2407 | 2500 | 2-5S | 12N14P | |
T-motor F60 P | 2207 | 2500 | 3-4S | 12N14P | |
3BHOBBY | 2207 | 2650 | 4S | 12S14P | |
BrotherHobby Returner | 2207 | 2700 | 4-5S | 12N14P | |
Lumenier RB2206-8 | 2206 | 2650 | 2-4S | 12N14P |
THE BASICS OF BRUSHLESS MOTOR
There are 2 major parts for a brushless motor called stator and a rotor. A picture is shown below for reference.
The stator is the stationary part of the motor(windings) and the rotor is the rotatory part of the motor(bell with magnets). Also there are a lot of other minor things such as bearings, coil, magnets, shafts etc.

A motor size is based on the stator size (diameter and height).. For example if a motor is sized as 2207, it means that the stator is 22mm in width and has 07mm in stator height.
Also there is something called as a KV of a motor. What it means is that the speed at which the motor rotate for every volt applied to the motor, theoretically.
Thrust to Weight Ratio
Brushless motors come in all shapes and sizes. The general rule of thumb is to aim for 2:1 thrust to weight ratio. You aren’t going to be able to do hard core racing with it. The higher the better obviously. The thrust to weight to ratio depends mostly on the size of the quads themselves.
There are pre built quads such as from Diatone Crusader GT which has a thrust to weight ratio of 8:1. There are people who have achieved 13:1. But there are certain limitations for the motors, because they can only spin so fast and spinning them any faster makes them inefficient.
Even for a photography rig you should aim at least for 3 or 4:1 in case you decide to upgrade your setup in the future or add an HD camera or a bigger battery for longer flight times or something, then you’ll have some reserve power left to compensate.
For a drone racing beginner 4 or 5:1 thrust would be the sweet spot. If you’re on a tight budget then build a beast of a quad and limit the throttle limit on Betaflight or the transmitter.

Quad Motor Sizes – Taller and Wider stators
A motor is indicated by a set of 4 numbers like 2207 or 2306 or whatever it may be. It denotes the diameter and the height of the rotor in millimetre (mm). The bigger the motor gets the higher the thrust it generates.
- Taller stator = higher top speed and terrible low speed handling
- Wider stator = lower top speed and better handling at lower speeds
The main cause is the increased magnetic field from the stators. The taller stators have larger magnets as compared to smaller and wider stators.
2207 vs 2306 motors
A good comparison would be the typical 2207 vs 2306 motors. It is a hugely debated topic as to which is better and one can’t be recommended over the other as both have their advantages and disadvantages which will be covered in another article.
Brushless Motor Size Chart
The motor selection is determined on how large you want to build your quad. Hence the name Frame size = Motor size.
By determining the frame size we can define how large of a motor we should use.
Frame size also limits the prop size and each prop requires a different motor to spin it and generate the thrust efficiently.
Also the KV of a motor plays an important role in the selection of the motor. As mentioned earlier higher KV draws more current.
The table below shows the nominal frames and quadcopter motor numbers:
Frame Size | Prop Size | Motor Size | KV |
---|---|---|---|
150mm and smaller | 3″ and smaller | 1105-1306 | 3000 and higher |
180mm | 4″ | 1806 | 2600-3000 |
210mm | 5″ | 2204-2208/2306 | 2600-3000 |
250mm | 6″ | 2205-2208/2306 | 2000-2300 |
300mm | 7″ | 2208/2212 | 1600 |
PERFORMANCE FACTORS
KV – Velocity Constant
Theoreticly KV represents the speed at which the motor rotates for every volt applied to the motor. For example if a motor is 2300kv with a 3S quadcopter battery motor applied to its ends then the motor will spin at 2600×12.60 =32,760 rpm (Revolutions per minute – number of turns in one minute), without propellers. The rpm decreases gradually because of air resistance.
Theoreticly KV represents the speed at which the motor rotates for every volt applied to the motor.
Higher the KV means lower resistance and higher current draw and lower efficiencies. Lower KV means higher resistance and lower current draw and considerably better efficiencies.
If you’re starting out somewhere around 2300-2400 KV would be desirable.
For example, if a motor is rated at 2300kv with a 3s battery voltage applied to it, then the motor will spin at 2300×12.60 =28,980 rpm without the propellers, and it is the maximum rpm it can attain at no load.
The rpm sharply decreases when a propeller is mounted because of air resistance offered to the motor while spinning the propeller.
Torque
Moving on the next factor that comes into picture is the torque produced by the motor. Torque is the spinning force or the rotatory force that spins the propeller. It doesn’t matter much if you’re starting out.
Motor torque is affected by factors such as:
1. Stator size- bigger the stator higher the torque
2. Materials such as quality of magnets and copper windings in the rotor
3. Motor construction factors such as air gaps between stator and rotor.
Torque produced by the motor significantly affects the performance of the quad. It also determines how the quad is going to feel for the inputs. Higher the torque produced by the motor, the more responsive the quad will perform.
Torque also governs how fast a quad change its direction mid-flight which will greatly help to do tighter turns in a race. Relatively if a motor produces less torque and is fitted with heavier props, the motor can’t spin the propeller and resulting in reduced efficiencies and also thrust. The current draw in an over propped motor will be significantly high.
The one major disadvantage of high torque motors are even though they feel more snappy and responsive to the controls they have bad oscillation. Since motors with high torque are able to change their rpm more rapidly they actually amplify the error (oscillation).
Oscillation is hard to get rid of in Betaflight even with PID tuning,especially on the yaw axis of the quad.
Efficiency
The efficiency of a motor is calculated by dividing the thrust produced by the motor at 100% throttle by the power produced by the motor.
This is measured by grams per watt (g/w). The higher this ratio, the more efficient the motor is essentially. We are not going to be flying 100% throttle the whole time; therefore it is important to consider the efficiency of the motor through the whole throttle range from 0% all the way up to 100% throttle.
Some motors may be efficient in the lower end of the throttle curve and some motors may be more efficient in the higher end of the throttle curve. Therefore it is important to choose the right motor depending on the style of your flying.
Current Draw
Current drawn by the motor is important because it helps us to determine the quadcopter esc size required for that particular motor.
For example, a 1104 motor draws 10A max at 100% throttle whereas some 2306 motors draw 40A max at 100% throttles. An esc must be selected accordingly for 20% more rating than the current drawn at 100% by the motor.
Ie; if a motor draws 30A max at 100% throttle, an esc rated for 36A constant current would be ideal.
There is also known as burst rating of an esc. It’s the maximum amps of current the esc can handle for a short period of time without damaging itself.
Temperature
Temperature or heat in general is a killer of motors over time. If the motors are exposed to prolonged heating, the magnets in the rotor lose their magnetic field strength over time. They demagnetize over time when exposed to constant heat and consequently resulting in a reduced lifespan of the motor.
The main reasons for a motor to heat are over propping and using higher throttles for long periods of time. If you’re a pro level drone racer, you will be running at higher throttles, but if you are just starting out and the motor heats then the motor is over propped.
But motor manufacturers compensate for this issue by designing cooling fins to help the motor to suck in air into the motor and cool itself equating to longer life spans, provided you don’t crash and destroy the motor beforehand.
OTHER FACTORS TO CONSIDER
N and P numbers

A typical 22xx or 23xx motor will have 12 poles and 14 magnets. This number will be denoted something like 12P14N. As depicted in the diagram, the poles are present on the stator and the permanent magnets are found on the rotor of a motor.
Single & Multi stranded wires
Single stranded wires as the name suggests is made of a single wire of copper whereas multi stranded wires are made of 3 smaller wires to replace the single thicker wire. Single stranded wires are thicker and handle heat produced much better when used on high voltage builds.
Multi stranded wires break or melt easily at higher operating temperatures. Typically multi stranded wires are more efficient because they pack the wires much tighter and closer together, therefore giving stronger magnetic fields and resulting in more powerful motors.
Magnets
The magnets in a motor play an important role in deciding how powerful a motor is going to be.
Cheap motors will have weaker magnets and produce less thrust as compared to an expensive motor which will have more powerful magnets.
Some higher-end motors even have curved magnets which are contoured to the shape of the rotor.
Magnets used in brushless motors are graded based on the magnetic strength such as N52, N54 etc…, the higher the stronger the magnetic field produced by the magnets.
Motor windings
Another factor to consider is the quality of the windings of the motor. If the motor has high quality copper windings they’re going to offer less resistance for the flow of currents and thus offering better efficiencies and longer flight times.
Motor Weight
The weight of a motor is governed by the size and materials of the motor. The bigger the motor the heavier it is. Keeping in mind the motors used on a 5” quad usually weigh with wires around 30-40 grams. There are some very light motors such as the Emax RSII which weigh around 25 grams for a 2306 motor with a couple of grams for the wires.
There are some very heavy motors such as the cobra 2204 motors which weigh around 34 grams. As they say, every gram counts, especially with the motors. Why? Because the moment arm increases the heavier the motor gets. Simply put it takes a significantly large amount of force to turn a quad with increase in every gram.
But that doesn’t mean lighter is better. Lighter motors are not as durable as the heavier ones because they would be made of lighter materials to save weight. Hence it all boils down to what are you going to use the motor for.
Motor mounting patterns
The mounting patterns of a motor also matter because it should be compatible with all the frames you choose to put the motor in. Most 5” quads these days use motor sizes from 2205 to 2407.
All the motors either have (16×16) mm or (16×19) mm mounting patterns. All the modern frames support all those mounting patterns and this shouldn’t be much of a concern.
The above image shows a brushless motor in a quad. The screw holes will be present on the stator of the motor. The above-shown motor or the stator has a 16×19 mm mounting pattern and uses 4 m3 screws for securing the motor to the frame.
FEATURES TO LOOK FOR IN MOTORS
Motor Shaft
Newer motors nowadays use hollow shafts as opposed to a solid shaft in an attempt to reduce the weight of the motor. This has its positives and negatives.
Hollow shafts obviously reduce the weight of the motor but they’re less durable during crashes.
You can’t replace shafts without replacing the whole rotor of the motor. For budget builders, hollow shafts are a bad thing but for those looking to save every gram hollow shafts are the way to go.

Air gap
Another thing for a better performing motor is the air gap between the stator and the rotor. The closer the rotor is to the stator (magnets to the windings) the more efficient it is in converting the current. The smaller the air gap the higher the thrust that motor produces as the stator slices through magnetic fields better.
Motor wires
The next thing that affects the performance of a motor is the wire gauge of the motor. The motors either use 20 Awg or 18Awg (American wire gauge). The Emax RS series claim that changing from a 22 gauge to a 20 gauge wire increased the power output by 5%. But this is no big deal when buying a motor and getting started in the hobby.
Retainer clips
The next thing we are going to talk about is the retainer clips or retaining methods of the stator and rotor. There are mainly 3 types we use in our hobby.
- E clip
- C clip
- Screw retainers
Each has their own advantages and disadvantages.
For example: E clips are difficult to remove without breaking the clip itself. Screw retainers are easily removable and hence giving easy access to the stator and rotor.
But screw retainers are prone to unscrewing and loosening over time under the constant vibration of the motor and also run the risk of over tightening the shaft and making it harder for the motor to spin. One clip can’t be recommended over the other. It all the depends on what the motor is going to be used for and its applications.
CW CCW motors
There are 2 types of motors- clockwise (CW) and counter clockwise (CCW) rotation motors. They vary only by the direction by which they rotate with the rest of the design parameters of the motor being the same. The below diagram shows a motor orientation for a quad, hex and octa drone. We can conclude that opposite side motors spin in the same direction. It is the same in hex and octa drones.
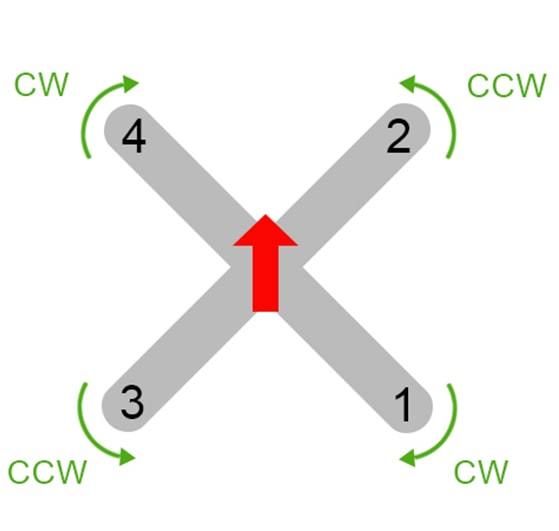

Naked bottom OR Closed bottom motors
The latest trend in quad motors are naked bottom motors. They save a lot of weight (2g in general), it may not seem much but that’s a lot in terms of drone racing. It may be the difference between winning a race or losing one.
Those are the pros of the naked bottom motors, there are also a few cons for these type of motors.
Firstly during a crash small stones and debris may get inside the bell and damaging the magnets and coils. Even pro racers crash often so it’s a good choice for beginner’s to buy a closed bottom motors when starting out in the hobby because they’re prone to crash more. The below photographs depict a naked and closed bottom motors.
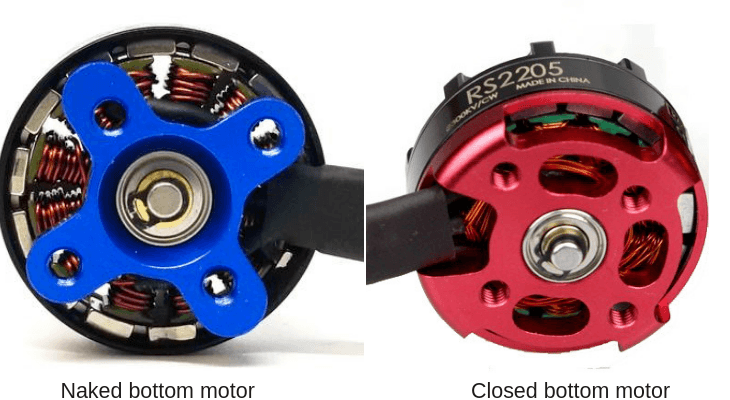
CONCLUSION
This article has tried to cover most of the basic aspects of a brushless motor for a quad. It will be modified in the future with some modifications to it as and when it is deemed necessary. There are so many options out there to choose from and we thought it should be covered in another article. We hope this article helped you in some way to help you gain some basic knowledge getting into FPV. Thank you for reading if you stayed all the way to the end.